LASER SCREED CONCRETE FLOORING
LASER SCREED CONCRETE FLOORING
Laser screed concrete flooring is a modern and highly efficient method of achieving level, smooth, and accurately finished concrete floors. This technology utilizes advanced machinery equipped with laser guidance systems to ensure precise placement and leveling of concrete across large surface areas. This process is commonly used in industrial, commercial, and even some residential construction projects where high-quality flooring is essential.
Key Steps in Laser Screed Concrete Flooring:
Subgrade Preparation: The ground where the concrete floor will be poured is properly prepared by compacting the soil and ensuring it is at the desired elevation and grade.
Concrete Mix Design: A well-designed concrete mix is prepared, taking into account the specific requirements of the project, including strength, workability, and durability.
Placing Initial Concrete: A layer of concrete is placed on the prepared subgrade using traditional methods, such as a concrete pump or chute.
Laser Guided Screeding: This is the central process in laser screed concrete flooring. A laser screed machine, equipped with a laser leveling system, is used to spread and level the concrete with extreme precision. The laser system ensures that the concrete surface is perfectly flat and at the desired elevation.
Vibrating and Consolidating: After the initial leveling, the concrete is vibrated and consolidated using built-in vibrators on the laser screed machine. This step helps eliminate air pockets and ensures proper compaction.
Finishing and Smoothing: A combination of troweling and floating techniques is employed to further refine the surface and create a smooth and polished finish.
Joint Cutting and Filling: Control joints are cut into the surface to control potential cracking, and joint fillers are applied as needed to maintain the structural integrity and prevent debris accumulation.
Curing: Proper curing methods are employed to ensure the concrete gains strength and durability over time. This might involve covering the surface to retain moisture and control temperature.
Benefits of Laser Screed Concrete Flooring:
Precision: The laser-guided system ensures an extremely level and accurately finished surface, meeting tight tolerances.
Efficiency: Laser screed machines can cover large areas quickly and efficiently, reducing labor and time requirements.
Quality: The controlled process minimizes the risk of surface imperfections and inconsistencies, resulting in a high-quality finish.
Reduced Labor: The use of laser screeds significantly reduces the manual labor required for leveling and finishing concrete.
Durability: Properly leveled and consolidated concrete floors have improved durability and resistance to wear and tear.
Fast Turnaround: The rapid process and quick curing times enable faster project completion and reduced downtime.
Aesthetics: The precise leveling and finishing contribute to a visually appealing surface.
Laser screed concrete flooring has revolutionized the way large concrete floors are constructed, offering efficiency, accuracy, and quality that traditional methods often struggle to achieve. It has become a popular choice in various industries where reliable and robust flooring solutions are needed.
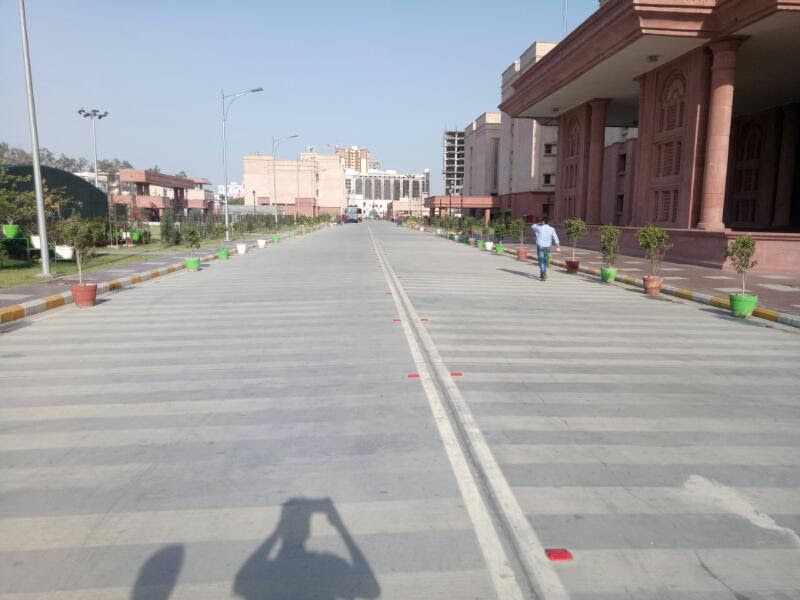
MAKE A DEFFRENCE CONCRETE FLOORING
Every day, Dramix R can help you to meet your deadlines. concrete reinforced with Dramix steel fiber successfully replaces the traditional and time consuming process of rebar placing. Dramix R eliminates all complexity with a stsndardized and easy to apply reinforcement solution. The result using Dramix R steel fibres saves 10- 15% of your time !
Technical Benats of Using CONCRETE FLOORING
- Increase in load bearing capacity due to redistribution of stresses.
- Reinforcement throughout the full depth offers excellent crack control
- Optimal resistance against impact and dynamic loads
- Phenomenal increase in post crack strength.
- Drastic improvement in fatigue resistance.
- No labor involvement to store and handle the reinforcement steel at job site.
- Avoids wastage of steel reinforcement providing and an increased economy rate of 5 to 10%.
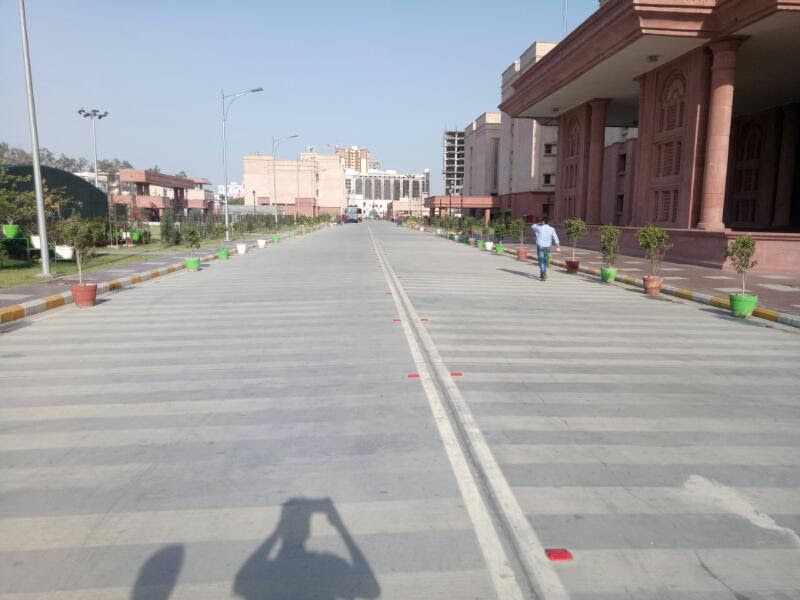